Countdown to 2024 - for ballast water treatment
February 2022
DESMI Ocean Guard has experienced great growth in recent years as the deadline for ballast water treatment approaches. Several marine engineers are helping the maritime industry get ready for the deadline in 2024.
MARLOG - DESMI OCEAN GUARD – ENGLISH VERSION – MASKINMESTEREN 1/2022. By Joel Goodstein
By September 8, 2024, the maritime industry must be ready to meet IMO requirements for ballast water treatment.
Close to 50,000 ships have been or must be equipped with ballast water treatment systems that will prevent microorganisms from becoming invasive species when they are transported around the globe in ballast water systems and discharged into foreign waters.
One of the suppliers is DESMI Ocean Guard, and the company has already delivered a large number of systems for ballast water treatment and has a filled-up order book until the deadline in 2024. »These are both retrofit and re-retrofit solutions. The latter is the replacement of existing ballast water systems that do not live up to the latest requirements or that can no longer be serviced because the supplier is no longer on the market,« says marine engineer, Bjarne Nørgaard Krogholm, who is Team Leader at DESMI Ocean Guard.
He heads the Engineering department that is responsible for 3D scanning onboard the ships and producing the necessary drawings and installation manuals for the customers. DESMI Ocean Guard develops, designs, builds, and commissions the facilities, but does not install them, so drawings and manuals are needed by shipping companies, shipyards, and installation companies when the ballast water systems are installed onboard the ships.
Small and large ships
Today, DESMI Ocean Guard is on the market with systems that can be adapted to the customers' special specifications. There are solutions for both small and large ships - from the smallest supply vessels to very large tankers and container ships.
»We have delivered systems to all types of ships, and our systems are approved to process from 35 cubic meters to 2,500 cubic meters of water per hour. If necessary, we can deliver even greater capacity by building parallel systems. The largest system so far has been a parallel system with 2 x 2100 cubic meters + 1 x 190 cubic meters for a separate ballast water tank on a big tanker« says marine engineer Nikolaj Brasch Baake, who joined DESMI Ocean Guard in 2020 as project manager after a few years at sea as a marine engineer on Maersk ships.
»In my daily tasks, I act as a liaison both internally and in relation to customers and external partners, advisors and classification societies, so I have a wide range of tasks. In my department, we take over a new project when there is an agreement with a customer. Then we manage the projects all the way through and have the systems delivered to the customers either at shipyards or where it has been agreed. The customers are responsible for the installation, and we then attend for commissioning and put the systems into operation, so I am involved in virtually all stages from start to finish, except for the initial sale,« he says.
At DESMI Ocean Guard, there is a team of project managers responsible for delivering the whole range of ballast water treatment systems.
»Additionally, we have colleagues in China, India, Singapore, and the USA, with whom we are in daily contact. We are an international company. In the morning we talk to customers and colleagues in Asia, and in the afternoon, we talk to South and North America,« says Nikolaj Brasch Baake.
UV and filter cleaning
Colleague Bjarne Nørgaard Krogholm joined DESMI Ocean Guard in 2015 when there were five employees in the company. Today, there are 35 in Denmark and 50 employees, when you count the foreign colleagues. Additionally, there are many employees in the sister company DESMI Pumping Technology that also take part in sales and production of DESMI Ocean Guard's ballast water systems, as well as several service engineers and aftersales coordinators employed in the sister company DESMI DeServe that commission and service the systems globally.
Bjarne Nørgaard Krogholm heads 12 employees in the Engineering department, six of them in India. »We have experienced a steadily increasing growth as the shipping industry approaches the deadline for installing ballast water treatment, and the expectation is that we will continue at a high level of delivery all the way until the deadline in 2024. The pressure to reach the deadline for all the affected ships has been further challenged by the COVID-19 pandemic, which has delayed many installations so that both we and many shipping companies will be busy all the way to the finish line in 2024,« he says.
Bjarne Noergaard in front of the CompactClean Ballast Water Management System
Two type approvals
DESMI Ocean Guard has two types of approvals of its systems - under both the IMO and the US Coast Guard. DESMI Ocean Guard’s systems for ballast water treatment are based on a combination of mechanical filter cleaning and UV radiation of the microorganisms.
The process of treating ballast water takes place in two steps: when the ballast water is pumped on board, and when it must go overboard again. When the seawater is taken onboard, it is first filtered at 20 µm and then exposed to UV radiation. When the water is sent overboard, it is irradiated with UV again. With this double process, there should be complete certainty that there are no living organisms left in the water.
»The cleaner the water, the more efficient the UV radiation. Therefore, the treatment begins with mechanical filtration before the UV treatment. The filter must effectively remove organisms and particles over 50 µm, which will otherwise reduce the effect of UV treatment, so when those particles are removed, we get the most effective UV treatment,« says Bjarne Nørgaard Krogholm. DESMI Ocean Guard has strived for a very compact design of its systems, which has also given name to the CompactClean solutions.
»The purpose of compact design is, of course, to accommodate the sometimes very limited space in a machine room full of other equipment. Typically, we arrive many years late with our systems in relation to the layout of the engine rooms. On some ships, there is not enough space in the engine room, and then we must find other places on board. On some ships, we deliver solutions located in deckhouses,« says Nikolaj Brasch Baake.
Special solutions
The existing pipe and pumping systems onboard are automated to varying degrees, but some ships’ systems are completely manually and locally operated. DESMI Ocean Guard's ballast water treatment systems contain a high degree of automation, but DESMI can also offer upgrades to the rest of the valve and pump control system.
»If the customers require it, we can deliver fully automated systems that can be integrated with the ships’ other control systems. We have our own automation department that can deliver exactly the solutions wanted, including customer-specific HMI solutions, and valve control systems for both new and existing valves. We also have extensive experience with the use and retrofit of frequency converters for the ballast water pumps, thereby saving energy, which equals a large amount of the energy used in the ballast water treatment. So, on some ships there is only a marginal increase in the total energy consumption,« says Bjarne Nørgaard Krogholm. In order to meet the bulk carrier market, a special system is offered, which meets the needs of this type of ship for extra fast deballast.
»Bulk carriers often get the cargo onboard very quickly - for example with a conveyor belt, and then the ship must be able to quickly get rid of ballast water, and this again requires that the UV system can keep up,« says Nikolaj Brasch Baake. For example, a bulk carrier may need 500 cubic meters of capacity per hour when ballast water comes on board, but a capacity for deballast of 1,000 cubic meters per hour, because ballast must be disposed of quickly when the cargo arrives on board with a conveyor belt. Here, DESMI Ocean Guard can deliver specially configured systems with a 500 cubic meter mechanical filter combined with a 1,000 cubic meter UV unit and thereby achieve a saving on installation costs, as the filter is only used for ballast.
Another of the solutions from DESMI Ocean Guard is the OptIMO system, which uses 30-35 percent less energy per cubic meter of UV-treated water when the system runs according to the requirements under the IMO type approval. Here you can increase the flow of water from 340 cubic meters under US Coast Guard requirements to 500 cubic meters at the same UV effect in IMO mode.
Compact systems
Other suppliers typically require additional systems, such as compressed air, cooling water and chemicals, but DESMI Ocean Guard’s solutions only require electricity and technical freshwater. The systems are also energy efficient and equipped with frequency converters, so they can go up and down in power efficiently. There is a continuous effort to develop new UV solutions that have high efficiency in relation to energy consumption, as is the case with the OptIMO solution.
»It has been exciting to be part of our business for some years now. Thereby, you get to know a technical area very well and get a deep knowledge of these technologies. It is a benefit for the company as well as for me because it opens up new opportunities,« says Bjarne Nørgaard Krogholm. Due to the currently high freight rates, shipping companies try to avoid docking with their ships in addition to the required Surveys every five years, and in some cases, DESMI Ocean Guard can offer installation at sea - without interrupting the ship’s agreed schedule.
»Some shipping companies can install ballast water systems during the fixed docks every five years, but as an alternative, we sometimes offer the possibility of installation while sailing. If the necessary prerequisites are met. You can both remove and install, for example, pipes and other components while sailing. We supply a step-by-step installation guide to the customer. Sometimes, it is possible to complete the installation during a few days’ port stay, so the shipping company completely avoids dock stays and can comply with the sailing schedule. Our service department will then visit the ship, to approve that the installations have been done according to our specifications and commission the system in collaboration with the ship’s crew, and review the system together with a classification inspector so the ship obtains its new D2 certificate,« says Nikolaj Brasch Baake.
Nikolaj Brasch in front of the CompactClean Ballast Water Management System
Doubled size
DESMI Ocean Guard has doubled in size in the two yers he has been employed, and there is an expectation that there will continue to be a new build market after the deadline for the existing ships in 2024.
»We are a company that is passionate about delivering good solutions, and I can use a lot of my experience as a marine engineer in my job. It is an exciting part of the industry with a lot of international contacts every day, and it is also necessary to navigate the cultural differences between customers and partners. You must know how to communicate with different people and learn when an agreement is an agreement. These are the conditions in a global industry, and that is an exciting part of the job,« says Nikolaj Brasch Baake.
»I still use many things from my marine engineer education - knowledge about pumps, project management, and finance. I probably did not value all those subjects equally during my education, but today I need to know what a contribution margin is. We cannot take money with us to work, so the whole financial side of our work is much more important than you might have thought when you were being educated,« says Bjarne Nørgaard Krogholm.
- Why is DESMI a MARLOG member?
DESMI wants to be visible and active in all relevant networks, collaborations and organizations in order to have the best possible knowledge of both current trends and future conditions in the industry - and in this way help to shape development. Especially, there is an interest in technological innovation and securing recruitment, including relevant education and training.
- What has DESMI gained so far from being part of MARLOG?
Improved network for customers, including shipping companies, and other partners, including suppliers and educational institutions. Exchange of experience with colleagues, competitors, customers and many others in the industry. Close connection with the current agendas: green transition, energy savings and digitization. Participation in job fairs etc. Through the dialogue in MARLOG, the company gets a better picture of its own position - commercially, technologically, and in terms of innovation.
- What does DESMI hope to gain from its MARLOG membership in the future?
Continued expanded cooperation with all relevant players in the industry, both in North Jutland, but also nationally. Securing the educational "food chains" for the industry. Initiation and participation in relevant technological and commercial development projects. As one of the major players in the industry, DESMI wants the opportunity to influence the industry in the right direction - which is now supported by MARLOG as a nationwide cluster organization.
Source: John Kristian Pedersen, Segment Director, DESMI
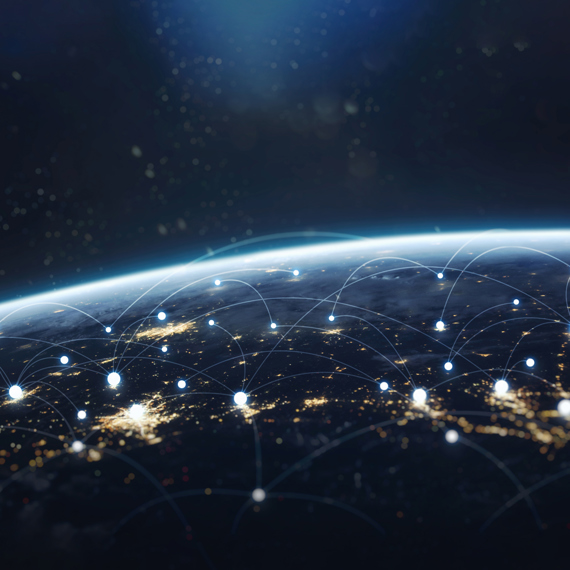