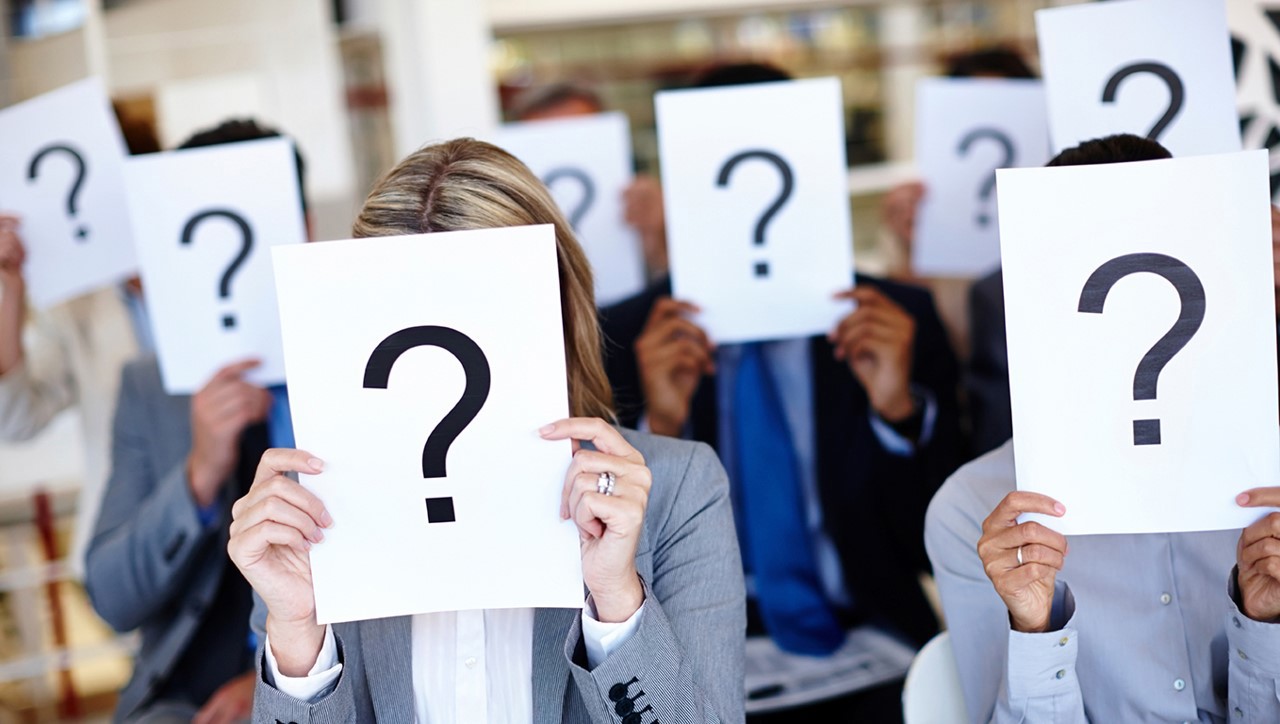
Save money with an effective Ballast Water Management Solution
Power consumption is often an important consideration when selecting Ballast Water Management equipment. Yet, while power consumption makes up a proportion of a ship’s operational expenditures (OPEX) over time, Ballast Water Management Systems are only operated a few percent of the time in a year.
So when comparing Ballast Water Management Systems, the difference in annual OPEX is actually insignificant. The following case example illustrates this point.
Bulk Carrier Operating Profile:
Consider a bulk carrier with a total ballast pump capacity of 1,000 m3/h with following operating profile:
l ballast tank capacity | 16,000 m3 |
Number of ballasting/ de-ballasting operations per year | 24 (ballast water passes through the treatment system 48 times per year) |
Hours per ballasting/de-ballasting operation | 16 hours |
Estimated specific fuel oil consumption of ship’s gensets | 0.224 kg/kWh |
According to the operating profile, the total ballasting and de-ballasting operating hours per year is 768 hours. If the vessel is operating only in IMO-regulated waters, the total fuel oil consumption per year for one CompactClean-1000 system (assuming an average power consumption of 86 kW) is 14.8 tons. In comparison, a system with a slightly lower average power consumption (e.g., 60 kW) consumes 10.3 tons of fuel oil per year.
From a cost perspective, if the price of fuel oil is 390.00 EUR per ton, the total fuel cost for operating the CompactClean-1000 system for one year is approximately 5,800.00 EUR, while the 60 kW system would cost 4,100.00 EUR, i.e. a difference of 1,700.00 EUR.
It should be noted that this case example does not consider holding time or flowrate restrictions in US mode, and as illustrated below the small fuel saving that can be obtained in IMO mode with a lower power consuming system is quickly converted into an additional cost when the same system occasionally has to be operated in its USCG mode.
CompactClean does not apply flow reduction to meet USCG discharge standards. But other, slightly lower power-consuming Ballast Water Management Systems as the one in this example, typically apply a 50% reduction in flowrate when ballasting and de-ballasting in US mode. In this example, it means the time required for ballasting and de-ballasting in one year would increase from 768 hours to 1,536 hours.
This increases the total fuel cost from approximately 4,100.00 EUR to 8,200.00 EUR, which is 2.400 EUR higher OPEX in a year than with the CompactClean.
Assuming the maximum power draw of a Ballast Water Management System is available on the ship during cargo operation, it is hard to argue that a Ballast Water Management System with low power consumption should be prioritised without carefully examining the system’s limitations. This is especially true in terms of hold time, flow restrictions and operating system complexity, which can easily create much more cost than the small saving obtained due to slightly lower power consumption.