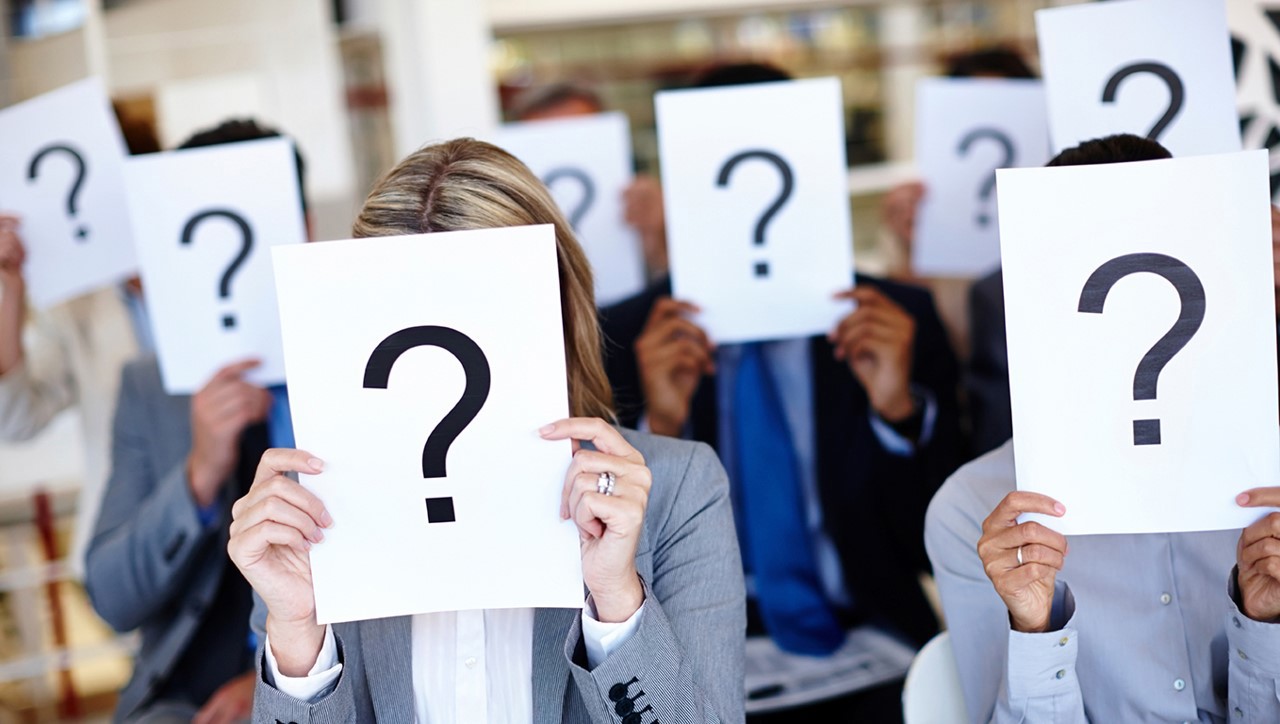
Selecting a Ballast Water Management System
Ships are carrying ballast water around the world to ensure stability, trim and structural integrity and the ballast water often originates from environmental ecosystems with different organisms than the ecosystem in which the ballast water is discharged. Ballast water management is needed in order to protect marine ecosystems around the globe.
Having a full understanding of the different Ballast Water Management technologies, their benefits and limitations, sets the foundation for making the right decision when selecting a Ballast Water Management System.
Below is highlighted 6 questions followed by answers to explain and elaborate on the area of Ballast Water Management.
BALLAST WATER MANAGEMENT MADE EASY
Your choice of ballast water management system can make a huge difference to your daily operation and lead to lost income. This story from the field will show you why operating with just one global operation mode instead of two, is what you want for your vessel.
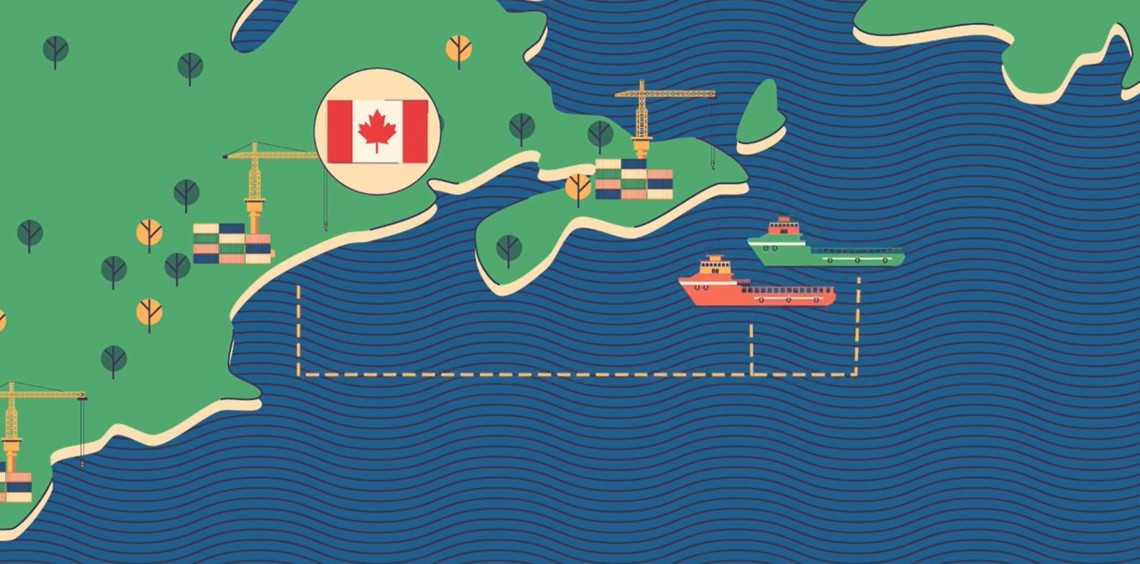